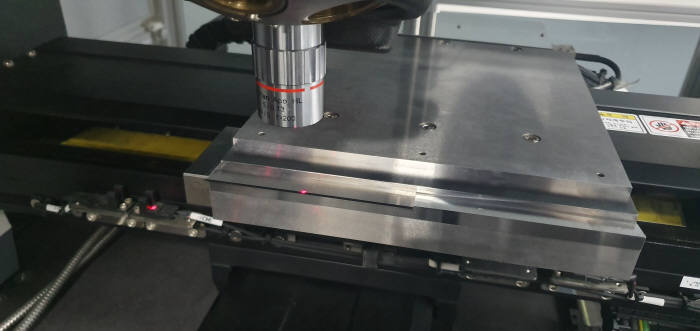
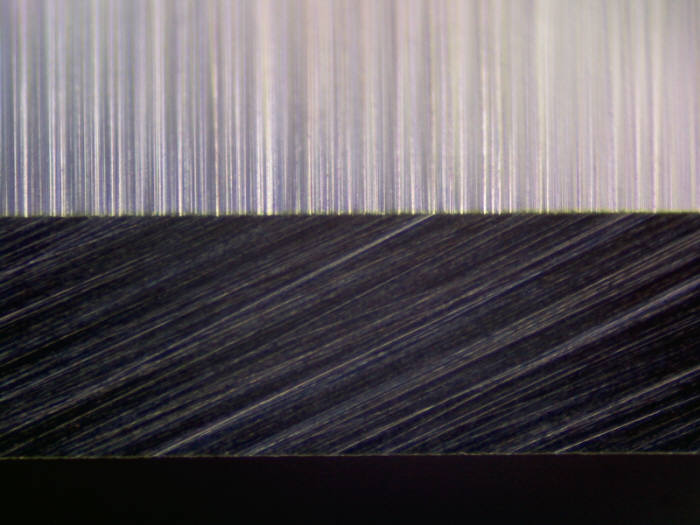
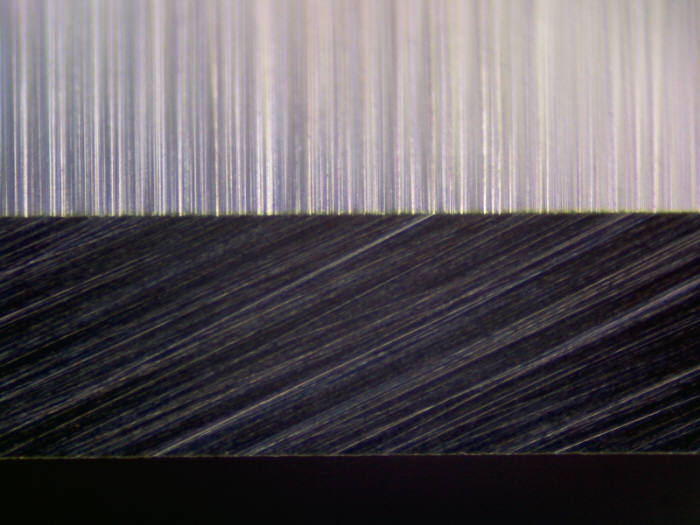
The world’s first ultra-precision cutting blade that combines electrolytic continuous dressing (ELID) grinding processing technology and femtosecond (10-15s, fs) laser processing technology has been developed for the first time in the world.
With the development of ultra-precision blades used for mass production of ultra-small electronic components such as LCD panels, OLED microfilms, and multilayer ceramic capacitors (MLCC), electronic component manufacturers are expected to improve quality and productivity.
21st Century Co., Ltd. (CEO Kim Seong-hwan) announced on the 24th that it was the first in Korea to develop a blade using ELID grinding processing technology and femtosecond laser processing technology and is currently conducting commercial tests on its production line with the goal of mass production within this year.
The company succeeded in applying femtosecond laser processing technology to ELID grinding processing technology, which was developed in 2017. 21st Century Co., Ltd. took this opportunity to secure ultra-precision blade processing technology that raised precision and durability by one level or more, and challenged the global ultra-fine and ultra-precision machining market led by advanced countries such as Germany and Japan.
ELID grinding uses a fine-grained diamond wheel and performs a dressing operation during grinding to achieve ultra-precise mirror surface grinding, so cemented carbide blades can be machined in nanometer units.
However, in ELID grinding, there is a problem of burrs (excessive parts in the shape of thin fins) at the tip of the blade, and blade wear and chipping (fine damage) occurs when cutting MLCC sheets for a long period of time. will follow.
21st Century Co., Ltd. integrates femtosecond laser processing technology and irradiates photon energy with a microwave width to minimize thermal effects during blade processing. In addition, by processing the blade edge more sharply, the load received in the process of cutting precision parts was reduced, thereby solving the existing blade problems.
The company utilizes hybrid-type next-generation processing technology to achieve △blade edge 0.8 μm → 0.2 μm △blade angle 30° → 6° △blade edge round type (round) → sharp type △ blade durability 100% → 150%, etc. It had the effect of improving blade performance.
An official from 21st Century Co., Ltd. said, “We are taking the stage of commercialization for the mass production of ultra-precision blades for precision electronic parts.” “Manufacturers can achieve productivity improvement and cost reduction effects by improving parts quality by reducing cutting load and increasing blade life.” said.
A company official also said, “For ultra-precision blades for precision electronic parts, machining precision, uniformity, edge shape, edge angle, and surface condition of the machining surface are key conditions for quality. It can be used for cutting various electronic parts such as MLCC.”